Aluminium-ekstrusieproses
Die extrusieproses van aluminiumlegering begin eintlik met die produkontwerp, omdat die produkontwerp gebaseer is op die gegewe gebruiksvereistes, wat baie finale parameters van die produk bepaal, soos die meganiese verwerkingsprestasie van die produk, oppervlakbehandeling en die gebruik van omgewingsvereistes. , hierdie eienskappe en vereistes bepaal eintlik die keuse van geëxtrudeerde aluminiumlegering.
Die eienskappe van geëxtrudeerde aluminium word egter bepaal deur die ontwerpvorm van die produk en die vorm van die produk bepaal die vorm van die extrusiematrijs.
Sodra die ontwerpprobleem opgelos is, begin die extrusieproses met extrusie gegiet in aluminiumstaaf, aluminium gietstaaf moet voor extrusie verhit word om dit sag te maak, die verhitting van goeie aluminium gietstawe word in die extrudervat binne geplaas, en dan deur hoë krag hidrouliese silinder stoot extrusie staaf, die voorkant van die extrusie staaf het 'n druk pad, soos verhitte sagte aluminiumlegering in dummy blok onder sterk druk van die vorm presisie giet extrusie giet.
Dit is waarvoor 'n vorm is: die vorm van die produk wat nodig is vir produksie.
Die prentjie is: 'n tipiese skema van die horisontale hidrouliese ekstruder
Die rigting van extrusie word van links na regs
Dit is 'n eenvoudige beskrywing van die mees gebruikte direkte ekstrusie van vandag. Indirekte ekstrusie is 'n soortgelyke proses, maar daar is baie belangrike verskille.
In die indirekte extrusieproses word die matrijs op die hol extrusiestang geïnstalleer, sodat die mat na die onbeweeglike aluminiumstaaf gedruk word, wat die aluminiumlegering dwing om deur die mat in die hol extrusiestang te extrudeer.
In werklikheid is die ekstrusieproses soortgelyk aan die uitdruk van die tandepasta. Wanneer die druk op die geslote punt van die tandepasta toegepas word, word die silindriese tandepasta deur die sirkelvormige opening gedruk.
As die opening plat is, kom die uitgedrukte tandepasta as 'n lint uit.
Natuurlik kan komplekse vorms ook by openinge van dieselfde vorm uitgedruk word, byvoorbeeld gebruik koekmakers spesiaal gevormde buise om roomys uit te pers om allerlei fieterjasies te maak.
Alhoewel u nie baie nuttige produkte met tandepasta of roomys kan maak nie, kan u nie aluminium met u vingers in buise druk nie.
Maar u kan 'n kragtige hidrouliese pers gebruik om aluminium uit 'n gegewe vormvorm te extrudeer om 'n wye verskeidenheid nuttige produkte van byna enige vorm te produseer.
Die onderstaande figuur (links) toon die eerste gedeelte van die extruder aan die begin van die extrusie. (regs)
Die kroeg
Die aluminiumstaaf is die spasie van die extrusieproses. Die aluminiumstaaf wat vir extrusie gebruik word, kan solied of hol wees, gewoonlik silindries, en die lengte daarvan word deur die extrusiebuis bepaal.
Aluminiumstawe word gewoonlik gevorm deur giet, of deur smeed of poeier te smee. Dit word gewoonlik gemaak deur aluminiumlegeringsstawe met goeie allooi-samestelling te saag.
Aluminiumlegerings bestaan gewoonlik uit meer as een metaalelement. Uitgedrukte aluminiumlegerings bestaan uit spoorelemente (gewoonlik nie meer as 5%) (soos koper, magnesium, silikon, mangaan of sink) wat die eienskappe van suiwer aluminium verbeter en die ekstrusieproses beïnvloed.
Die lengte van aluminiumstaaf wissel van vervaardiger tot vervaardiger, wat bepaal word deur die finale vereiste lengte, extrusieverhouding, ontladingslengte en ekstrusietoelaag.
Standaardlengtes wissel gewoonlik van 660 mm tot 1830 mm. Buitendiameters wissel van 76 mm tot 338 cm, 155 mm tot 228 mm.
Direkte extrusieproses
[billet] [verwarmingsoond] [extrusiepers met matrijs] saag [strecher] [veroudering van overname]
Die diagram illustreer die basiese stappe om 'n aluminiumstaaf uit te druk

Wanneer die finale produkvorm bepaal word, word die toepaslike aluminiumlegering gekies, die vervaardiging van die extrusiematrijs voltooi en die voorbereiding vir die werklike ekstrusieproses voltooi.
Voorverhit dan die aluminiumstaaf en die extrusie-instrument. Tydens die extrusieproses is die aluminiumstaaf solied, maar het dit sag geword in die oond.
Die smeltpunt van aluminiumlegering is ongeveer 660 ℃. Die tipiese verhittingstemperatuur van die ekstrusieproses is oor die algemeen groter as 375 ℃ en kan so hoog as 500 be wees, afhangende van die ekstrusie-toestand van die metaal.
Die werklike extrusieproses begin wanneer die extrusiestang druk begin uitoefen op die aluminiumstaaf in die ingot.
Verskillende hidrouliese perse is ontwerp om oral tussen 100 ton en 15 000 ton te pers. Hierdie extrusiedruk bepaal die grootte van die extrusie wat deur die extrusiemasjien vervaardig word.
Uitgedrukte produkspesifikasies word aangedui deur die maksimum deursnitgrootte van die produk, soms ook deur die omtreksdeursnee van die produk.
Wanneer die extrusie pas begin het, word die aluminiumstaaf onderhewig aan die reaksiekrag van die vorm en word dit korter en dikker totdat die uitbreiding van die aluminiumstaaf beperk word deur die muur van die blokke;
As die druk dan steeds toeneem, het die sagte (steeds soliede) metaal geen plek om te vloei nie en begin dit uit die vormvorm van die vorm na die ander kant van die vorm te druk, wat die profiel vorm.
Ongeveer 10% van die aluminiumstaaf (insluitende die aluminiumstaafvel) is in die loopvat agter, die ekstrusieproduk word uit die vorm gesny en die oorblywende metaal in die loop word skoongemaak en herwin. Nadat die produk die vorm verlaat, die daaropvolgende proses is dat die warm ekstrusieproduk geblus, bewerk en verouder word.
Wanneer die verhitte aluminium uit die vorm deur die gatsilinder geëxtrudeer word, vloei die metaal in die middel van die aluminiumstaaf vinniger as die rand. Soos die swart streep in die illustrasie toon, word die metaal om die rande agtergelaat om te herwin soos 'n oorblyfsel.
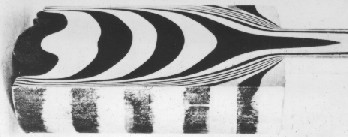
Die extrusiesnelheid hang af van die legering wat gepers word en die vorm van die uitlaatgat. Die gebruik van harde legering om komplekse vormstowwe te pers, kan so stadig wees as 1-2 voet per minuut. Met sagte legerings kan eenvoudige vorms tot 180 voet per minuut of meer gedruk word.
Die lengte van die extrusieproduk hang af van die aluminiumstaaf en die vormuitlaatgat. 'N Deurlopende extrusie kan 'n produk tot 200 voet lank produseer. Die nuutste vorm-extrusie, wanneer die geëxtrudeerde produk die extruder verlaat, word op die skuif geplaas (gelykstaande aan die vervoerband)
Volgens die verskillende legering, is die extrusie uit die produkverkoelingsmodus: verdeel in natuurlike verkoeling, lug- of waterverkoeling, maar blus. Dit is 'n belangrike stap om die metallografiese prestasie van die produk na veroudering te verseker. Die geëxtrudeerde produk word dan oorgedra na 'n koue bed.
Maak reg
Na afbranding (afkoel) word die geëxtrudeerde produk reguit gemaak en reguit gemaak deur 'n draagbaar of 'n reguitstrek (rek word ook geklassifiseer as koudbewerking na extrusie). Uiteindelik word die produk deur die transporttoestel na die saagmasjien oorgedra.
Saag
Tipiese saag van eindprodukte is die saag van 'n produk tot 'n spesifieke handelslengte. Sirkelsae word vandag die meeste gebruik, soos draai-armsae wat lang stukke geëxtrudeerde materiaal vertikaal sny.
Daar is ook sae wat aan die bokant van die profiel gesny is (soos 'n elektriese verstekzaag). Die saagtafel is ook 'n nuttige saagtafel met 'n skyfzaaglem van onder na onder om die produk te sny en dan weer tot onder. van die tabel vir die volgende siklus.
'N Tipiese afgewerkte sirkelsaag is 16-20 sentimeter in deursnee en het meer as 100 tande van hardmetaal. Groot saaglemme word gebruik vir extrusies met 'n groot deursnee.
Die selfsmerende saagmasjien is toegerus met 'n stelsel wat smeermiddel aan die saagtand aflewer om optimale saagdoeltreffendheid en die oppervlak van die saag te verseker.
'N Outomatiese pers hou die gedeeltes in plek vir saag en die saagreste word vir herwinning versamel.
Veroudering:
Sommige geëxtrudeerde produkte benodig veroudering om optimale sterkte te behaal, daarom word dit ook veroudering genoem. Natuurlike veroudering word by kamertemperatuur gedoen. Kunsmatige veroudering word in die verouderingsoond uitgevoer. Tegnies word dit neerslagintensiewe fase-hittebehandeling genoem.
Wanneer die profiel uit die extruder geëxtrudeer word, word die profiel halfvast, maar dit word vinnig solied wanneer dit afgekoel of geblus word (hetsy lug- of watergekoel).
Nie-hittebehandelde aluminiumlegerings (soos aluminiumlegerings met toegevoegde magnesium of mangaan) word versterk deur natuurlike veroudering en koudbewerking. Die behandelbare aluminiumlegering (soos aluminiumlegering met koper, sink, magnesium + silikon) kan beter sterkte en hardheid verkry. deur die hittebehandeling van die metaalmetografiese struktuur te beïnvloed.
Veroudering is ook om die deeltjies van die versterkte fase eweredig te skei om die maksimum opbrengsterkte, hardheid en elastisiteit van die spesiale legering te verkry.
Bale
Of verouderingsoond of veroudering by kamertemperatuur, na volle veroudering, die profiel word oorgedra na die oppervlakbehandelings- of diepverwerkingswerkswinkel of bale gereed vir vervoer na die klant.
Mense vra ook
Plaas tyd: 20 Maart 2020