Процесс экструзии алюминия
Процесс экструзии алюминиевого сплава фактически начинается с дизайна продукта, поскольку дизайн продукта основан на заданных эксплуатационных требованиях, которые определяют многие конечные параметры продукта, такие как характеристики механической обработки продукта, характеристики обработки поверхности и использование требований к окружающей среде. , эти свойства и требования фактически определяют выбор экструдированного алюминиевого сплава.
Однако свойства экструдированного алюминия определяются конструктивной формой продукта. Форма продукта определяет форму экструзионной головки.
После решения проектной проблемы практический процесс экструзии начинается с экструзии алюминиевого стержня, алюминиевый стержень для литья должен быть нагрет перед экструзией, чтобы размягчить его, слиток шенга слитка алюминиевого литья с хорошим нагревом помещается в цилиндр экструдера внутри, а затем под высоким давлением. силовой гидравлический цилиндр, толкающий экструзионный стержень, передний конец экструзионного стержня имеет нажимную подушку, такой как нагретый мягкий алюминиевый сплав в фиктивном блоке под сильным давлением от пресс-формы прецизионного формования экструзией.
Для этого нужна форма: форма продукта, необходимая для производства.
На картинке: принципиальная схема типичного горизонтального гидравлического экструдера.
Направление выдавливания слева направо.
Это простое описание наиболее широко используемой сегодня прямой экструзии. Непрямая экструзия - это похожий процесс, но с некоторыми очень важными отличиями.
В процессе непрямой экструзии головку устанавливают на полый экструзионный стержень, так что матрица прижимается к неподвижной алюминиевой заготовке стержня, заставляя алюминиевый сплав выдавливаться к полому экструзионному стержню через головку.
По сути, процесс выдавливания похож на выдавливание зубной пасты. Когда давление прикладывается к закрытому концу зубной пасты, цилиндрическая зубная паста выдавливается через круглое отверстие.
Если отверстие ровное, выдавленная зубная паста выходит в виде ленты.
Разумеется, сложные формы можно выдавить и через отверстия одинаковой формы. Например, кондитеры используют трубочки особой формы для выдавливания мороженого и делают всевозможные оборки.
Хотя из зубной пасты или мороженого не получится приготовить много полезных продуктов, нельзя пальцами выдавить алюминий в тюбики.
Но вы можете использовать мощный гидравлический пресс для выдавливания алюминия из формы заданной формы для производства широкого спектра полезных продуктов практически любой формы.
На рисунке ниже (слева) показана первая секция экструдера в начале экструзии. (верно)
Бар
Алюминиевый стержень - это заготовка процесса экструзии. Алюминиевый стержень, используемый для экструзии, может быть сплошным или полым, обычно цилиндрическим, а его длина определяется экструзионной трубкой.
Алюминиевые прутки обычно изготавливаются путем литья, ковки или порошковой ковки, а также путем распиливания прутков из алюминиевого сплава с хорошим составом сплава.
Алюминиевые сплавы обычно состоят из более чем одного металлического элемента. Экструдированные алюминиевые сплавы состоят из микроэлементов (обычно не более 5%) (таких как медь, магний, кремний, марганец или цинк), которые улучшают свойства чистого алюминия и влияют на процесс экструзии.
Длина алюминиевого стержня варьируется от производителя к производителю, что определяется конечной необходимой длиной, степенью экструзии, длиной выгрузки и припуском на экструзию.
Стандартная длина обычно составляет от 26 дюймов (660 мм) до 72 дюймов (1830 мм). Внешний диаметр варьируется от 3 дюймов (76 мм) до 33 дюймов (838 мм), от 6 дюймов (155 мм) до 9 дюймов (228 мм).
Процесс прямой экструзии
[заготовка] [нагревательная печь] [экструзионный пресс с матрицей] пила [растяжка] [старение поверх]
На схеме показаны основные этапы экструдирования алюминиевого стержня.

Когда форма конечного продукта определена, соответствующий алюминиевый сплав выбран, изготовление экструзионной головки завершено, и подготовка к собственно процессу экструзии завершена.
Затем предварительно нагрейте алюминиевый стержень и инструмент для выдавливания. В процессе экструзии алюминиевый пруток остается твердым, но размягчается в печи.
Температура плавления алюминиевого сплава составляет около 660 ° C. Типичная температура нагрева в процессе экструзии обычно превышает 375 ° C и может достигать 500 ° C, в зависимости от условий экструзии металла.
Фактический процесс экструзии начинается, когда экструзионный стержень начинает оказывать давление на алюминиевый стержень в слитке.
Различные гидравлические прессы предназначены для сжатия от 100 до 15000 тонн. Это давление экструзии определяет размер экструзии, производимой экструзионной машиной.
Характеристики экструдированного продукта указаны по максимальному размеру поперечного сечения продукта, иногда также по окружному диаметру продукта.
Когда экструзия только началась, алюминиевый стержень подвергается воздействию силы реакции изложницы и становится все короче и толще, пока расширение алюминиевого стержня не будет ограничено стенкой цилиндра для слитка;
Затем, когда давление продолжает увеличиваться, мягкому (все еще твердому) металлу некуда течь и он начинает выдавливаться из формующего отверстия формы к другому концу формы, образуя профиль.
Около 10% алюминиевого стержня (включая оболочку алюминиевого стержня) остается в цилиндре для слитка, продукт экструзии вырезается из кристаллизатора, а оставшийся металл в цилиндре для слитка очищается и перерабатывается. последующий процесс заключается в закалке, механической обработке и старении продукта горячей экструзии.
Когда нагретый алюминий выдавливается из кристаллизатора через цилиндр для слитков, металл в центре алюминиевого стержня течет быстрее, чем по краю. Как показано черной полосой на иллюстрации, металл по краям остается позади для вторичной переработки. остаток.
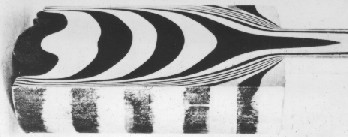
Скорость экструзии зависит от сжимаемого сплава и формы выпускного отверстия фильеры. Использование твердого сплава для сжатия материалов сложной формы может происходить со скоростью 1-2 фута в минуту. С мягкими сплавами простые формы можно прессовать со скоростью 180 футов в минуту и более.
Длина экструзионного продукта зависит от алюминиевого стержня и выпускного отверстия формы. Непрерывная экструзия может производить продукт длиной до 200 футов. Последняя форма экструзии, когда экструдированный продукт выходит из экструдера, помещается на ползун (эквивалент конвейерной ленты);
В зависимости от сплава, экструзия из режима охлаждения продукта: разделена на естественное охлаждение, воздушное или водяное охлаждение, но закалка. Это ключевой этап для обеспечения металлографических характеристик продукта после старения. Экструдированный продукт затем переносится в холодная постель.
Выпрямить
После закалки (охлаждения) экструдированный продукт выпрямляется и выравнивается с помощью вытяжного устройства или выпрямителя (вытяжка также классифицируется как холодная обработка после экструзии). Наконец, продукт транспортирующим устройством переносится на пильный станок.
Распиловка
Типичная распиловка готового продукта - это распиловка продукта до определенной коммерческой длины. Циркулярные пилы являются наиболее широко используемыми сегодня, как и пилы с поворотным рычагом, которые разрезают длинные куски экструдированного материала вертикально.
Есть также пилы, нарезанные сверху профиля (например, электрическая торцовочная пила) .Также полезный стол для пилы, стол для пилы с дисковой пилой снизу вверх, чтобы разрезать продукт, а затем диск пилы обратно вниз таблицы для следующего цикла.
Типичная законченная дисковая пила имеет диаметр 16-20 дюймов и имеет более 100 твердосплавных зубьев. Большие пилы используются для экструдеров большого диаметра.
Самосмазывающийся пильный станок оснащен системой, которая подает смазку к зубу пилы, чтобы обеспечить оптимальную эффективность пиления и поверхность пилы.
Автоматический пресс удерживает секции на месте для распиловки, а остатки распиловки собираются для вторичной переработки.
Старение:
Некоторым экструдированным изделиям требуется старение для достижения оптимальной прочности, поэтому его также называют старением. Естественное старение осуществляется при комнатной температуре. Искусственное старение проводится в печи для старения. Технически это называется термической обработкой с интенсивным осаждением.
Когда профиль выдавливается из экструдера, он становится полутвердым, но вскоре становится твердым при охлаждении или закалке (с воздушным или водяным охлаждением).
Алюминиевые сплавы без термической обработки (например, алюминиевые сплавы с добавлением магния или марганца) упрочняются естественным старением и холодной обработкой. Алюминиевый сплав с термической обработкой (например, алюминиевый сплав с медью, цинком, магнием + кремнием) может получить лучшую прочность и твердость. за счет воздействия термической обработки на металлографическую структуру сплава.
Кроме того, старение заключается в равномерном разделении частиц упрочненной фазы для получения максимального предела текучести, твердости и эластичности специального сплава.
Тюки
Будь то печь для старения или старение при комнатной температуре, после полного старения профиль передается в цех обработки поверхности или в цех глубокой обработки или в тюки, готовые к транспортировке заказчику.
Тоже спрашивают
Время публикации: 20 марта 2020 г.