ODM Factory China Factory Price Custom Made Billet 6061-T6 Aluminum Heavy-Duty Supercharger Bracket Kit
We believe that long term partnership is a result of high quality, value added service, rich experience and personal contact for ODM Factory China Factory Price Custom Made Billet 6061-T6 Aluminum Heavy-Duty Supercharger Bracket Kit, we could solve our customer problems asap and do the profit for our customer. If you need good service and quality , pls choose us , thanks !
We believe that long term partnership is a result of high quality, value added service, rich experience and personal contact for aluminum metal handle, China Bracket, custom aluminum handle, custom metal bracket, Supercharger Bracket, If any item be of interest for you, make sure you let us know. We’ll try our best to satisfy your requirements with high quality merchandise, the best prices and prompt delivery. Please feel free to contact us at any time. We are going to reply you when we receive your inquiries. You should note that samples are available before we start our business.
Custom locker name plates
Material | zinc alloy, alum alloy |
Process | - Zinc alloy+dissolve+diecast+galvanized+ovening - by die-cast by die-cast machine- further combined with polishing/galvanizing or painting process to achieve the parts. |
Application | Nameplate for wardrobe |
NW | 180g |
Mold | Tool opening |
LT | 15 days |
Type | OEM Parts |
Mass production Lead time | 4weeks |
Weihua technology (custom locker name plates manufacturers) fine technology, fast proofing speed, support customer customization, product diversity, quality after-sales service.
What are the commonly used materials for making metal nameplates?
The nameplate is mainly used for furniture and mechanical products. Its existence is not only a sign, but also represents the culture, deposits and strength of the enterprise.So, our business friends, for the hardware sign production, the requirements are more strict.In particular, the sign with what material, is the most concerned about the topic.
Here, in order to let you know more, we here to share the specific material, sign with what?
1, smooth sign: picture or board surface is oily, very smooth sign.
2. Luminous material label: luminous material label (that is, we usually say neon).
3, metal nameplate: in the case of no specially designated plate, the metal as the plate or the main material of the alloy plate.
4, acrylic sign (acrylic) : acrylic material to do the main material of the board sign.
5, electric light plate: the use of light emitting diode or luminous tube to achieve monochrome or color performance.The light-emitting diodes and their performance can be divided into five categories: luminous electro-optical plate, LCD, LED, CRT, FDT, etc.
For China technology mainly undertake trademark, sign orders.Products mainly include computers, mobile phones, audio, refrigerators, air conditioners and other digital home appliances are used on the copper, aluminum, stainless steel nameplates, plastic signs, mirror display, three-dimensional signs, crystal drop plastic signs, nameplate processing, copper signs research and development of all kinds of modern difficult technology metal nameplates, welcome your consultation!
You may also like:nameplate for headlight;Please click to view ~
If you are interested in getting in touch with a our sales rep click here
The main process shows as below
Step 1:Zinc alloy
Step 2:Advanced dissolved device
Step 3:Hi-precision die-cast tooling
Step 4:Large scale die-cast device
Step 7:Professional inspectors and packaging workers
Step 5:Galvanizing line
Step 8:Structured parts
Step 6:Industry oven, hi temp, low temp, constant temp
“Our 40,000 square meters facility has the capabilities to meet all your extrusion aluminum, logo plates,precision stamping needs coupled with multiple fabrication options to produce high-quality products solutions. ”
― WEIHUA
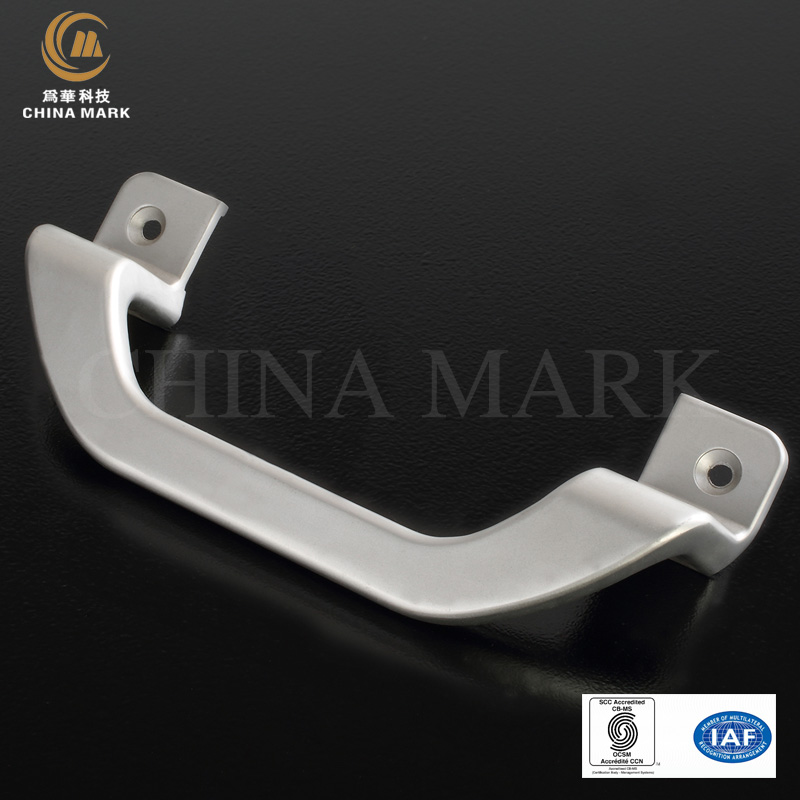
Although many zinc alloy castings can be used in the as-cast state, surface treatment is required in some cases to protect the castings from corrosion on the one hand, and also play a decorative role on the other hand to make the appearance more beautiful.
The following introduction of zinc alloy die castings:
One. What are the main surface treatment processes for zinc alloy castings?
①Plating: The zinc alloy castings that have just been polished look like chromium plated. Zinc alloy castings can also be directly plated with chromium. Direct chromium plating can increase the hardness and wear resistance of the casting, reduce the friction factor and improve the corrosion resistance.
②Painting: zinc alloy can be coated with various paints. For some cheaper parts, acrylic paint with weak adhesion and acid corrosion components can be used. For parts that require high corrosion resistance, it is best to use epoxy resin paint or various amine-based paints, and bake after painting.
③Metal spraying: The metal spraying method is to coat the surface of the processed parts with a thin metal film under high vacuum. Metal spraying can simulate the appearance of copper, silver, brass, gold, etc. This process is mostly used for die castings.
④ Anodizing treatment: The anodizing treatment of zinc alloy castings is carried out in the anodizing treatment solution and at a voltage not exceeding 200V. Anodizing treatment can effectively improve the corrosion resistance of zinc alloys.
Second. can aluminum alloy replace zinc alloy?
The answer is no. Because the performance of zinc alloy die-casting is better, it can die-cast precision parts with complex shapes and thin walls. The surface of the castings is smooth and the dimensional accuracy is high. It has good compression resistance and wear resistance. Zinc alloy die-castings can well accept various Kinds of surface treatments (plating, spraying, painting, etc.)
By comparing the two alloy materials, we will find that aluminum alloy cannot replace zinc alloy, because the strength, hardness and formability of zinc alloy are much better than aluminum alloy.
Three. How to identify a good zinc alloy?
1. High purity, low zinc ingot impurity content, based on high-purity zinc raw materials. To
2. Low melting point: The melting point of a good zinc alloy is controlled at 380-390°C.
3. Less zinc dross: less zinc dross is produced when melting.
4. Knock it off to see the section. If the section is more delicate, it is generally better.